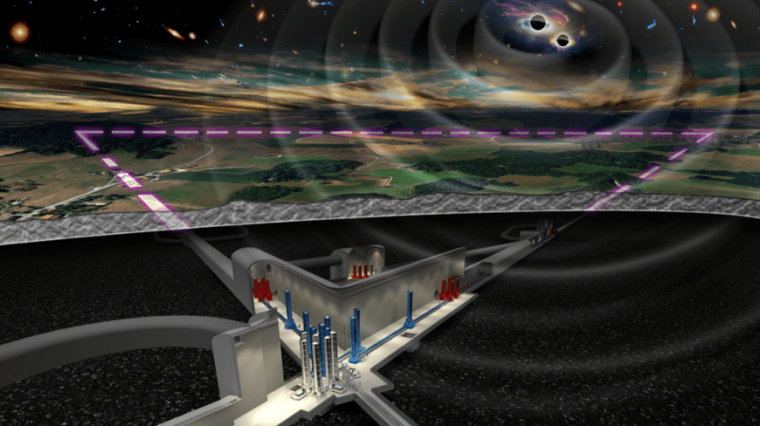
- Light
- Forschung
Published: | By: Siefke, Walther, Winkler
Why a new gravitational wave detector is essential
The measurement of gravitational waves has not only confirmed Einstein's theory of general relativity, but has also given us insights into cosmic events such as the merging of black holes and neutron stars. Gravitational waves thus provide a completely new approach to astronomy as well as fundamental insights into the origins of our universe. In order to investigate these phenomena in detail, exceptionally sensitive detectors are required that can capture even the weakest signals.
The planned Einstein Telescope (ET) is a third-generation gravitational wave detector, which should enable a significant increase in the performance of current observatories. The current plan envisages the construction of several interferometers with arm lengths of ten kilometers at a depth of 250 to 300 meters. The embedding in the ground is intended to significantly reduce the ambient noise, among other things through vibration absorption and stable foundation conditions. This enables the detector to resolve the finest variations in space-time. At the same time, the high demands on the technology pose new challenges for the optimization of the detector components.
-
Interferometer as a gravitational wave detector
Gravitational waves are distortions of space-time caused by extreme cosmic events such as the merging of black holes. They propagate through the universe at the speed of light, causing minimal stretching and compression of space. A typical gravitational wave leads to a relative change in length of around 10-21. For comparison: the diameter of the earth could fluctuate by around 10 femtometers (fm) as a result of such a wave - that corresponds to the size of an atomic nucleus! The tiny changes in length are measured using an interferometer by splitting a laser beam into two arms using a beam splitter. The laser beams are then reflected by mirrors and brought together again in the beam splitter. Normally, the two laser beams interfere in such a way that they cancel each other out - similar to the way the peaks and valleys of a water wave neutralize each other. However, if a gravitational wave causes a slight change in length in one of the arms, the interference pattern of the returning beams changes. This shift is then used to precisely calculate the change in arm length.
Schematic illustration of the stretched micromirror system: The radiation pressure of the laser positioned under the mirror counteracts the force of gravity.
Graphic: Trad Nery, M. 2022Challenge: Noise - the role of radiation pressure
As the sensitivity of the measuring devices increases, so do the challenges for noise suppression. The interferometer is confronted with various sources of interference, which are superimposed on the difficult-to-detect measurement signal as so-called noise. In the low-frequency range in particular, various factors such as seismic vibrations and atmospheric changes must be taken into account. These disturbances can affect the stability of the interferometer mirrors and make it difficult to distinguish between genuine gravitational wave signals and environmental influences.
Another problem is the instability of the photon flux generated by the laser. Even the smallest changes in laser power, i.e. changes in the brightness of the laser, cause a varying force effect on the mirrors (see Fig. 1) - the so-called radiation pressure. This ultimately leads to a low-frequency noise (radiation pressure noise) in the output signal of the measurement. The forces acting in this process are tiny - in the order of nanonewtons, comparable to the weight of a particle of dust - and yet must be recorded with the highest precision. This requires a sensor that is extremely light and therefore extremely small.
Micromirror innovation
At the Max Planck Institute for Gravitational Physics in Hanover, a novel concept based on a micro-oscillator has been developed to precisely control laser power. The core of this concept is an opto-mechanical element developed and realized by the Microstructure Technology Group at the Institute of Applied Physics in Jena. The basis is an ultra-light micromirror (D = 320 μm), which reacts extremely sensitively to changes in radiation pressure thanks to an extremely flexible mounting. The highly reflective micromirror is suspended horizontally on ultra-thin spring arms and is held against gravity by the radiation pressure of the laser. Its extremely high reflectivity of over 99 % protects the mirror from damage by the laser itself. If the photon flux and thus the radiation pressure against the mirror changes, the position of the mirror also changes. This shift is measured using interferometry and used as a feedback signal to control the laser power. Due to this active feedback loop, the laser power can be stabilized extremely precisely, which considerably reduces the noise source of the gravitational wave detector. However, the geometry and reflectivity of the sensitive micromirrors demand a great effort in the manufacturing process.
The close-up shows a section of an SOI wafer with through-holes in which micromirrors are mounted. Each micromirror has a diameter of 320 μm and is held in place by helical silicon springs specially designed for lightweight construction and the required low stiffness.
Image: M.WaltherHighest precision in manufacturing: Breakthrough in vapor HF etching of micromirrors
This high sensitivity of the micromirrors also creates challenges: even small air movements can cause the microstructure to vibrate or even destroy it, making the entire manufacturing process extremely sensitive to environmental conditions.
Together with the company memsstarExternal link, researchers from the Microstructure Technology Group have now succeeded for the first time in producing these filigree micromirrors on a silicon-on-insulator (SOI) wafer platform. First, the nano-optical structures required for the resonant mirrors and the flexible mounting structures were created in a thin crystalline silicon layer and the handling wafer was removed locally using a chemical-physical dry etching process. The exposed silicon dioxide sacrificial layer was then removed at memsstarExternal link using a special hydrofluoric acid (HF) gas phase etching process, allowing the micromirrors suspended from the spiral springs to be released. This innovative approach enables the production of extremely fine structures that span large areas (approx. 1 cm2) relative to the micromirror (see Fig. 2&3). Each micromirror is held by three spiral threads hanging over a 10 mm cut-out. These filaments of crystalline silicon are only 2 × 20 μm thick and therefore around 200 times finer than a human hair.
The high sensitivity of these filaments to the smallest air turbulence and vibrations makes the production and assembly of these ultra-light optical components a challenging task. Despite these challenges, HF gas phase etching has proven to be promising and shows the potential to realize even more complex micromirror designs. The plan is to produce such mirrors on even finer springs - this time up to 2 × 0.2 µm thick.
Conclusion
The manufacture of such micromirrors developed by Jena researchers in the Microstructure Technology Group of the IAP is a major innovation in the control and stabilization of laser power. The process technology developed is an important milestone for ultra-sensitive measurement techniques such as those required for the detection of gravitational waves and at the same time opens the door to a new era of high-precision industrial measurement methods.
Project name: “GT-4-ET” Glass Technologies for the Einstein Telescope
Funding: This research is supported by the GT-4-ET project, a collaboration between the Max Planck SocietyExternal link and the Fraunhofer-GesellschaftExternal link.
Duration: 2022-2025